Френският институт за слънчева енергия INES е разработил нови PV модули с термопластика и естествени влакна, получени в Европа, като лен и базалт. Учените имат за цел да намалят екологичния отпечатък и теглото на слънчевите панели, като същевременно подобряват рециклирането.
Рециклиран стъклен панел отпред и композит на бельо на гърба
Изображение: GD
От PV Magazine France
Изследователи от Националния институт за слънчева енергия във Франция (INES)-подразделение на френската алтернативна енергия и Комисията за атомна енергия (CEA)-разработват слънчеви модули, включващи нови био-базирани материали отпред и задна страна.
„Тъй като въглеродният отпечатък и анализът на жизнения цикъл вече се превърнаха в основни критерии при избора на фотоволтаични панели, снабдяването на материали ще се превърне в решаващ елемент в Европа през следващите няколко години“, казва Анис Фуини, директор на CEA-INES , в интервю за PV Magazine France.
Aude Derrier, координаторът на изследователския проект, заяви, че нейните колеги са разгледали различните материали, които вече съществуват, за да намерят такъв, който да позволи на производителите на модули да произвеждат панели, които подобряват производителността, издръжливостта и разходите, като същевременно намаляват въздействието върху околната среда. Първият демонстратор се състои от слънчеви клетки на хетероюнкция (HTJ), интегрирани в изцяло композитен материал.
„Предната страна е направена от полимер, изпълнен с фибростъкло, който осигурява прозрачност“, каза Дерие. „Задната страна е направена от композит на базата на термопластици, в които е интегрирано тъкане на две влакна, лен и базалт, което ще осигури механична якост, но също така и по -добра устойчивост на влажност.“
Лентът се получава от Северна Франция, където цялата индустриална екосистема вече присъства. Базалтът е снабден другаде в Европа и се изтъква от индустриален партньор на INES. Това намали въглеродния отпечатък със 75 грама CO2 на ват, в сравнение с референтен модул със същата мощност. Теглото също беше оптимизирано и е по -малко от 5 килограма на квадратен метър.
„Този модул е насочен към PV на покрива и интеграция на изграждане“, каза Дерие. „Предимството е, че той е естествено черен на цвят, без да е необходим заден лист. По отношение на рециклирането, благодарение на термопластиците, които могат да бъдат премахнати, разделянето на слоевете също е технически по -просто. "
Модулът може да бъде направен без адаптиране на текущите процеси. Derrier каза, че идеята е да се прехвърли технологията на производителите, без допълнителни инвестиции.
„Единственият императив е да има фризери, които да съхраняват материала и да не започват процеса на кръстосано свързване на смолата, но повечето производители днес използват Prepreg и вече са оборудвани за това“, каза тя.
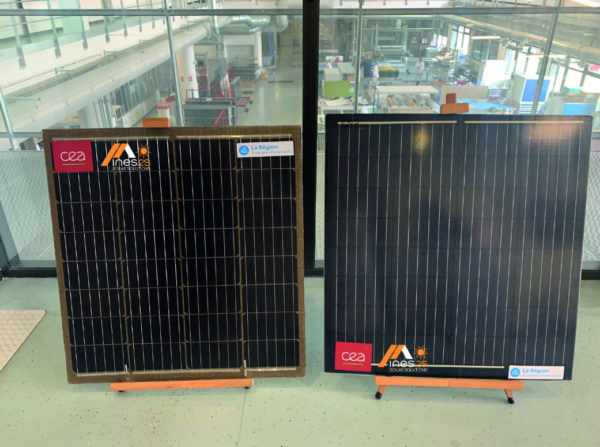
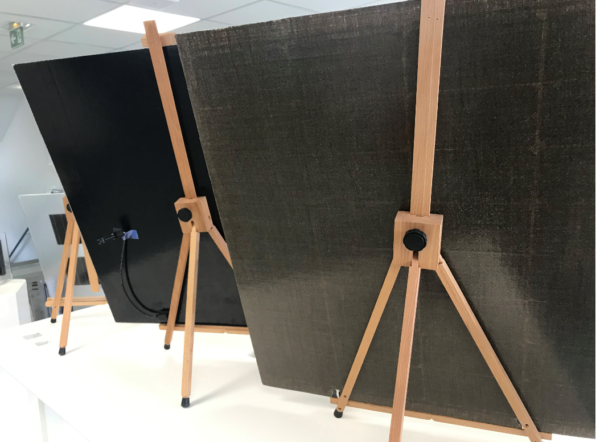
„Работихме върху втория живот на стъклото и разработихме модул, съставен от повторно използвано 2,8 мм стъкло, което идва от стар модул“, каза Дерие. „Използвахме и термопластичен капсулант, който не изисква омрежване, което следователно ще бъде лесен за рециклиране, и термопластичен композит с ленени влакна за устойчивост.“
Задното лице без базалт на модула има естествен цвят на бельо, който може да бъде естетически интересен за архитектите по отношение на фасадна интеграция, например. В допълнение, инструментът за изчисляване на INES показа 10% намаление на въглеродния отпечатък.
„Сега е наложително да се поставят под въпрос фотоволтаичните вериги за доставки“, каза Джуини. „С помощта на региона на Rhône-Alpes в рамките на Международния план за развитие, затова отидохме да търсим играчи извън слънчевия сектор, за да намерим нови термопластици и нови влакна. Помислихме и за настоящия процес на ламиниране, който е много енергийно интензивен. "
Между налягането, натискането и фазата на охлаждане, ламинирането обикновено продължава между 30 и 35 минути, с работна температура от около 150 ° С до 160 С. С.
„Но за модули, които все по-често включват еко проектирани материали, е необходимо да се трансформира термопластиката на около 200 C до 250 C, като се знае, че HTJ технологията е чувствителна към топлината и не трябва да надвишава 200 C“, каза Дерие.
Изследователският институт се обединява с специалиста по термокомпресия на базата на Франция Roctool, за да намали времето за цикъл и да прави форми според нуждите на клиентите. Заедно те са разработили модул със задно лице, направено от полипропилен тип термопластичен композит, към който са интегрирани рециклирани въглеродни влакна. Предната страна е изработена от термопластика и фибростъкло.
„Процесът на индукция на Roctool на Roctool дава възможност бързо да загрявате двете предни и задни плочи, без да се налага да достигате 200 ° С в сърцевината на HTJ клетките“, каза Дерие.
Компанията твърди, че инвестицията е по -ниска и процесът може да постигне време за цикъл от само няколко минути, като същевременно използва по -малко енергия. Технологията е насочена към композитни производители, за да им даде възможност за производство на части от различни форми и размери, като същевременно интегрират по -леки и трайни материали.
Време за публикация: юни-24-2022